Fuel Economy Engine Oils: Scientific Rationale and Controversies
Abstract
Since a significant part of energy losses in the internal combustion engine comes from viscous dissipation, the trend has shifted toward low-viscosity oils from SAE 40 and 50 in the 1960s-1980s to current SAE 20 and lower viscosity grades. Use of low viscosity engine oils significantly reduces energy losses in the main bearing and piston/bore systems, while tribological stresses on the valvetrain - especially in flat-tappet cammed engines - may increase. This makes a strong argument for deploying new classes of friction modifiers and antiwear additives. However, development of a balanced formulation is not as straightforward as it appears, and numerous pitfalls may be encountered due to additive interactions. Another serious problem is that the definition of “fuel-economy engine oil” is rather vague, as it depends on choice of reference oil. Nowadays, the assessment of fuel economy is based on the Sequence VIE or VIF tests using a 2012 3.6L GM V6 gasoline engine. It is not unexpected that the results of this test turn to be largely misleading when extrapolated to modern heavily boosted low-displacement engines. Hence, many OEM-specific fuel economy tests also exist and different engine designs often produce controversial results. Furthermore, the “fuel economy” performance of the same oil in the same engine may change dramatically depending on the driving cycle. For instance, low viscosity oil may boost fuel economy at cruising speeds (high speed / low load limit) and degrade fuel economy during aggressive city driving (low speed / high load).
All the aforesaid circumstances are to be taken into account when trying to harmonize normative performance claims with customer expectations.
Introduction
New fuel economy standards for automobiles erected by governments in the G20 major economies and change in customer preferences driven by high fuel prices together with carbon taxes put increased pressure on car makers. In the USA, National Highway Traffic Safety Administration (NHTSA) and Environmental Protection Agency (EPA) have recently issued the Safer Affordable Fuel-Efficient (SAFE) Vehicles Rule that sets tough fuel economy and carbon dioxide standards. These standards apply to passenger cars and light trucks and set a moving target that is going to increase 1.5% in stringency each year from model years 2021 through 2026. Noteworthy, recognizing the realities of the marketplace, the expectations bar has been lowered to 40.4 mpg projected overall industry average required fuel economy in MY 2026, compared to 46.7 mpg projected requirement under the 2012 standards. The latter was again lower than the initial 2025 EPA targets of 62 mpg announced a decade ago – which was soon afterwards reduced to 56 mpg.
This shows that the progress is rather painful and the overambitious targets may not be achieved without a solid technological foundation and powerful financial incentives to drive the change.
Other markets follow the same trend, see Fig. 1.
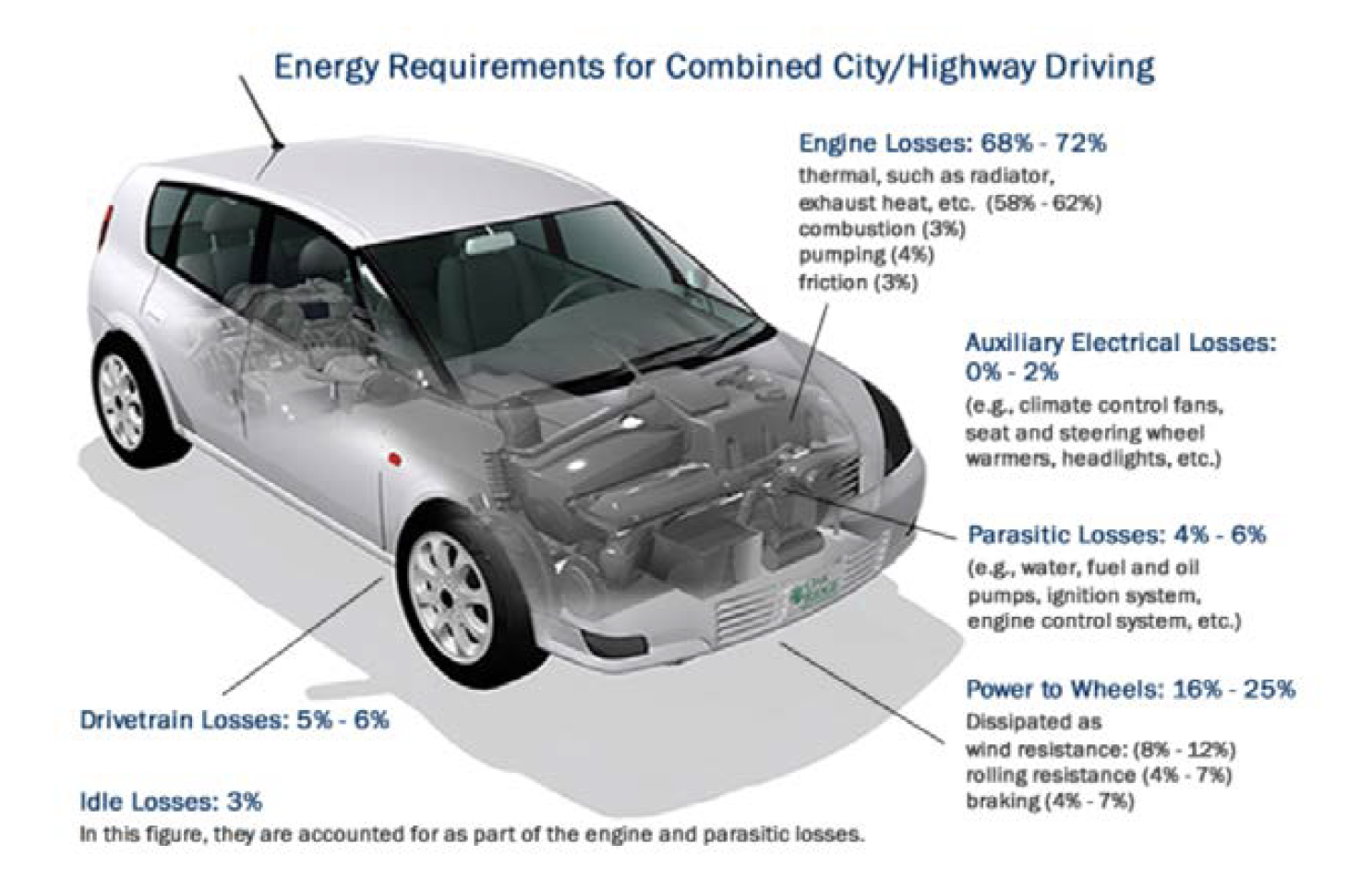
Fig.1 Comparison of fuel economy standards in key vehicle markets (Source: ICCT, September 2019)
In Europe, the European Parliament and the Council adopted Regulation (EU) 2019/631 that sets CO2 emission performance standards for new passenger cars and new vans for 2025 and 2030. From 2021, the EU fleet-wide average emission target for new cars is set at 95 g CO2/km. This corresponds to a fuel consumption of around 4.1 l/100 km (57.4 mpg) of petrol or 3.6 l/100 km (65.3 mpg) of diesel. Today’s average CO2 emissions for new cars sold in EU is around 120 g CO2/km. Car manufacturers pay the penalty is €95 for each g/km in excess of the target.
Japan’s new fuel economy standards issued a year ago set a target for average fleet gasoline-equivalent fuel economy at 25.4 kilometers per liter (59.8 mpg) by 2030, some 30% improvement over today’s fleet average.
These political and economic factors intensify research and development efforts taken by major OEMs in their pursuit for better fuel efficiency. Apart from concerted efforts on powertrain electrification and the use of alternative energy sources to reduce greenhouse gas (GHG) emissions, a big emphasis is made on understanding tribological aspects of energy losses in powertrain and utilizing current advancements in lubrication engineering and coatings to minimize those losses. To encourage such eco-innovation, manufacturers are granted “emission credits” for deployment of innovative technologies that should - based on independently verified data - result in reduced CO2 emissions even though the test procedure used for vehicle type approval fails to demonstrate any effect. Besides that, manufacturers are granted “super credits” for putting on the market zero- and low-emission cars (BEV, PHEV) emitting less than 50 g CO2/km.
Development costs, material costs and production costs are always important factors when market potential of one or another approach is to be assessed.
Approximately one third of fuel consumption in cars is due to friction losses [1] with powertrain friction being one of the chief culprits, see Fig. 2.
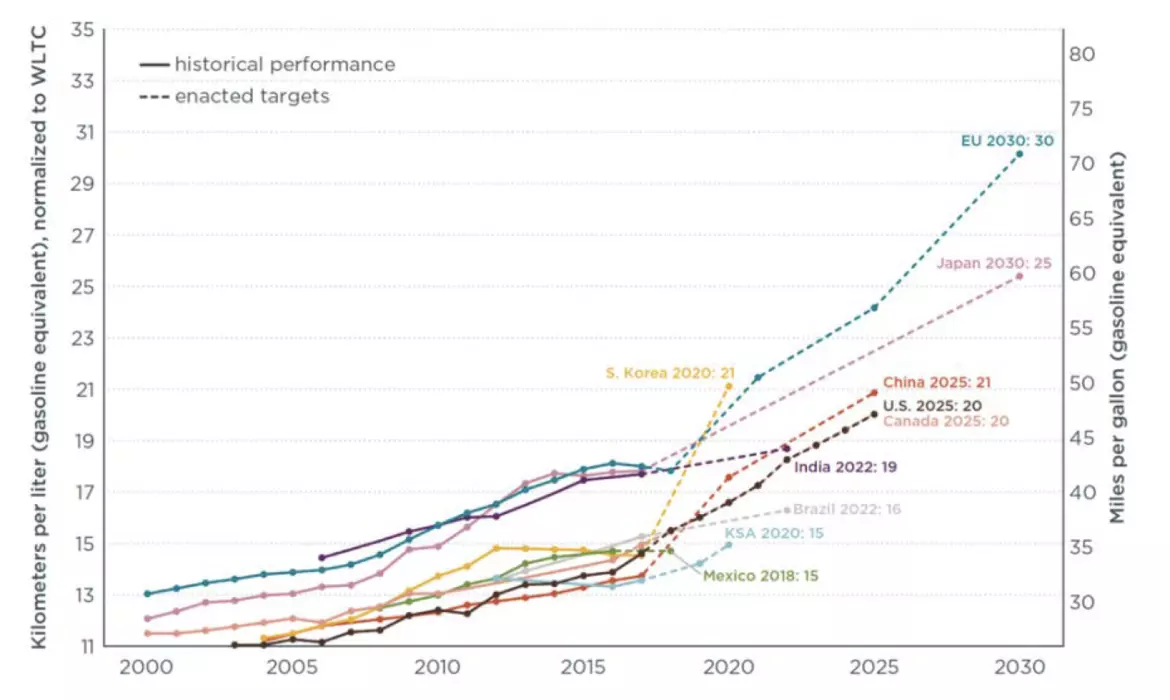
Fig.2 Energy losses in passenger cars (Source: www.fueleconomy.gov)
Therefore, the development of low friction powertrains is viewed as an important goal [1-3].
Role of motor oil in low friction powertrain development
Automotive engines are believed to operate predominantly in the hydrodynamic regime [4-6]. Therefore, by reducing lubricant viscosity, one can reduce engine friction and improve vehicle fuel economy. Fig. 3 explains how this strategy works: on the left-hand side is shown the actual torque curve of a typical production 1.6L GDI engine, and on the right-hand side is shown the friction torque curve for the same engine measured using a motored rig. Friction “eats up” around 1/10th of the useful torque the engine can produce. The fact that friction torque increases with engine speed proves the hydrodynamic lubrication regime. Therefore, changing to a lower viscosity lubricant helps reduce friction torque at high rpm.
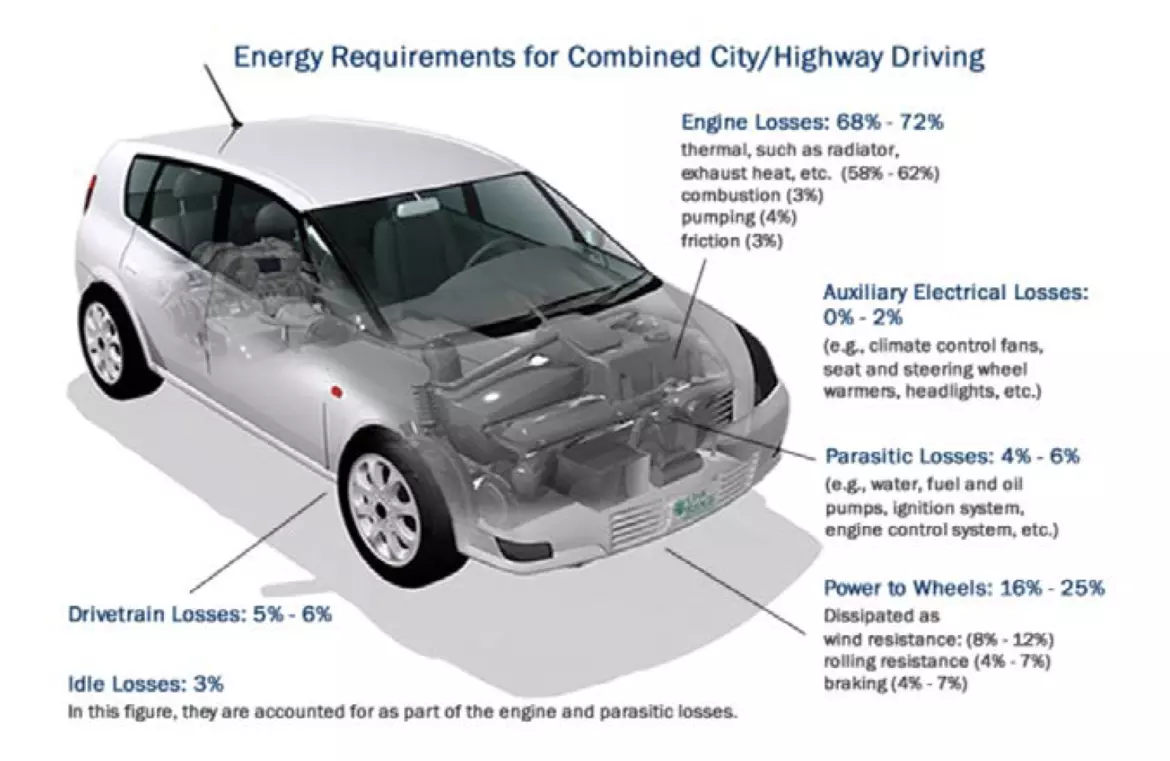
Fig.3 The torque curve (l.h.s.) and the friction torque curve (r.h.s.) for a production 1.6L i4 GDI engine. The primary engineering strategies for friction reduction are also shown.
Over the past two decades, there has been a steady trend toward lower viscosity lubricants, see Fig. 4. Thus, SAE J300 standard has been revised in 2015 to include three new lighter viscosity grades, SAE 16, 12 and 8. Heavier PCMO grades SAE xW-40, xW-50 and xW-60 are becoming niche products. The ILSAC GF-6 specification does not even include viscosities over SAE 30. Automotive gear lubricants follow suit: SAE J306 standard has been revised in 2019 adding SAE 75, 70 and 65 viscosity grades.
For passenger cars, a change from the legacy SAE 10W-40 grade to 0W-20 brings on average 5% improvement in fuel economy under the WLTP test conditions, and the subsequent migration to 0W-8 can bring additional 5%, provided that engine hardware can safely handle such a low viscosity. For heavy duty trucks the effect is much smaller: by switching from the legacy SAE 15W-40 to 5W-20, one saves no more than 2% under the ESC conditions, and even less under the ETC conditions. Many older HDDE designs are not capable to work with low viscosity oil.
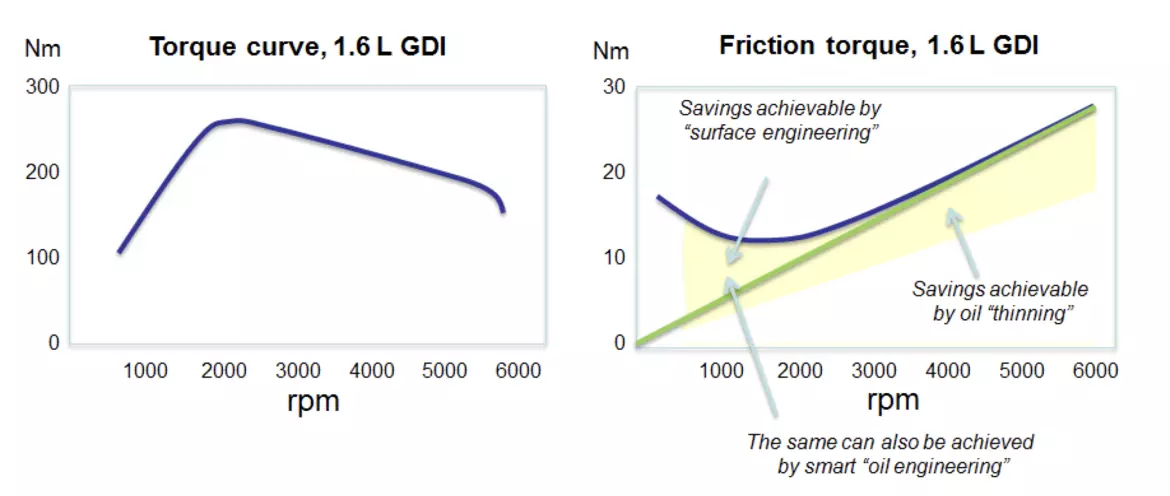
Fig.4 The continuing trend toward lower viscosity and lower SAPS lubricants
However, there is a primary obstacle to lowering lubricant viscosity further and further: it is wear [7-11]. The hydrodynamic lubricant film thickness is directly proportional to lubricant viscosity. Therefore, to maintain the hydrodynamic lubrication regime, one will have to alter surface finish specifications and upgrade oil pump and oil filtration system [7]. Without that, the risk of excessive wear is real and cannot be ignored, see Figs. 5-6
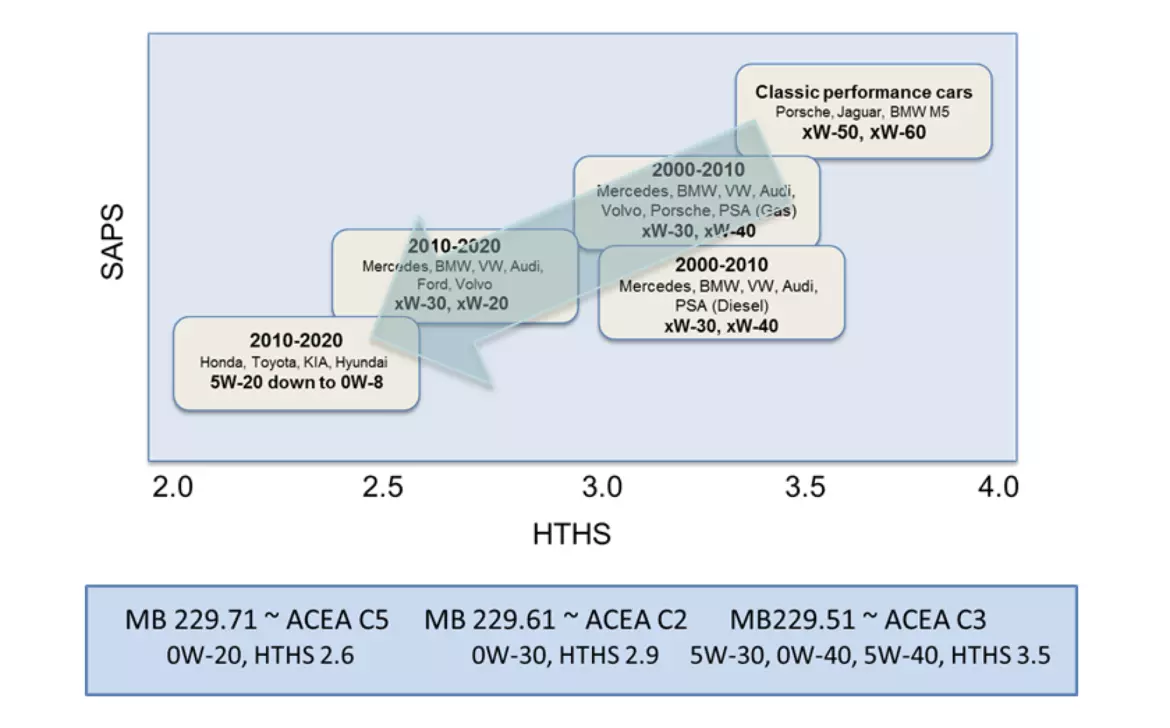
Fig.5 Simulated ΔBSFC and bearing health maps for a modern passenger car engine (after D.E. Sander et al. [8])
Fig. 5 shows the simulated ΔBSFC map for a modern passenger car engine and simulated bearing health map for the same. In the middle, the change in BSFC on changing from SAE 0W-20 (the left hand side) to 0W-8 (in the middle) is shown, the green area corresponding to improved fuel economy, the red area – to degraded fuel economy. Upto 20% reduction in BSFC is feasible. Unfortunately, the maximum effect is restricted to the wrong part of the map: medium-to-high engine speeds and low load. Such conditions apply to an engine revving up at idle. Close to the engine “sweet spot”, the effect on BSFC is reduced to 10%. However, the most troublesome observation is the red area at low rpm and high engine load, since this does not only signify a degraded fuel economy but also an elevated risk of wear [5,7-12]. This is confirmed by the main bearing health simulation.
Similar trends have been observed for heavy duty diesel engines, see Fig. 6. In fact, the mismatch is even more obvious in this case, since the maximum fuel saving effect comes at low load and high rpm, while the most wear occurs at high load and low speed, close to engine sweet spot. For many engines, troubles start already when changing from legacy API CJ-4 or its backward compatible successor API CK-4 to lighter FA-4 engine oil. At the same time, some new engines – e.g. from Scania and DAF – can safely use oils as light as 5W-20 and even 0W-16.
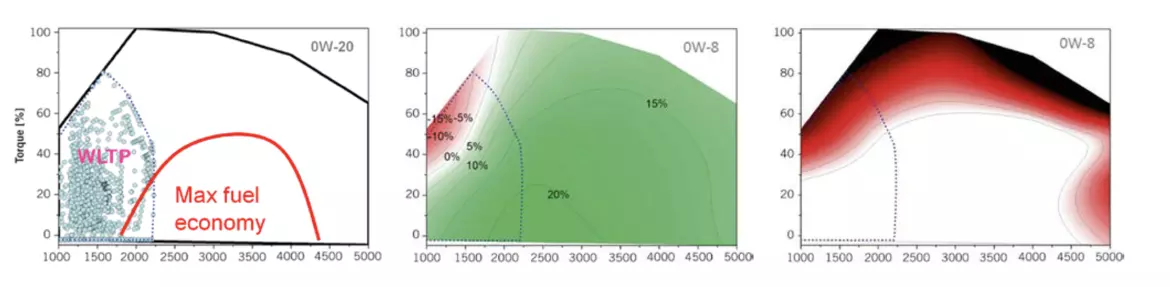
Fig.6 Potential wear issues with ultralow viscosity HDEO (after P. Klejwegt et al. [9])
The above examples show that it is under the low speed - high load conditions that lubricant film may fail. Problems at high speed are mostly associated with inadequate oil pump capacity and can be addressed by using variable pumps. At high engine speeds, inertial forces acting on the reciprocating group and cavitation effects also play an increased role. This may cause problems with the small end of the connecting rod/wrist pin interface and bearings. In general, lower viscosity lubricants tend to be less prone to cavitation.
Since the hydrodynamic film collapses when there is no relative motion between the rubbing surfaces, wear problems associated with the introduction of low viscosity lubricants are further aggravated due to automatic start-stop technology [13,14]. Use of electric oil pumps and roller bearings for camshaft and balancer shaft helps mitigate the issue. Roller bearing supported crankshafts were also tried but found impractical.
Crankcase lubricant formulations can be fine-tuned for optimal performance under specific conditions. For instance, motor oil can be designed to perform best at high engine speeds and temperature, as is the case with racing oils. However, racing oil wouldn’t be a good choice for on-road cars in stop-and-go urban traffic. On the contrary, one can design motor oil to perform best in stop-and-go city traffic, but then it may fail to earn its resource-conserving “Donut”.
Unlike racing oils, mainstream lubricants are formulated to balance a large number of different properties, a sort of conscious and unavoidable paradigm shift from “being best at something” to “being good enough at everything. Since the fuel efficiency is viewed as an extremely important performance aspect – in fact, many OEM approvals explicitly demand it – the transition to lower viscosities will continue. It should be recognized, however, that fuel economy oils do not make much economic sense for the end consumer – we talk about a fuel saving of 100 Euros or so compared to a risk of 1000 Euros if the oil is too thin and causes excessive engine wear. However, the benefit of these oils accrues to the car manufacturers. If their vehicles can save 1-2% fuel by using a special fuel economy lubricant, then that OEM can drastically reduce the amount of fines they may need to pay.
Use of friction modifiers in crankcase lubricants
Increased lubricant performance requirements explain a steady increase in the market share for synthetic lubricants over the past two decades. Synthetic base oils have multiple advantages: better property consistency, higher oxidation stability, better flow properties at low temperature, low volatility, etc., see Fig. 7 Combined with proper additives, synthetic base oils can be used to manufacture lubricants with outstanding properties. One type of additives deserves special mentioning as fuel economy engine oils are concerned: friction modifiers. Friction modifiers are an indispensable tool for “smart oil engineering”, see Fig. 3.
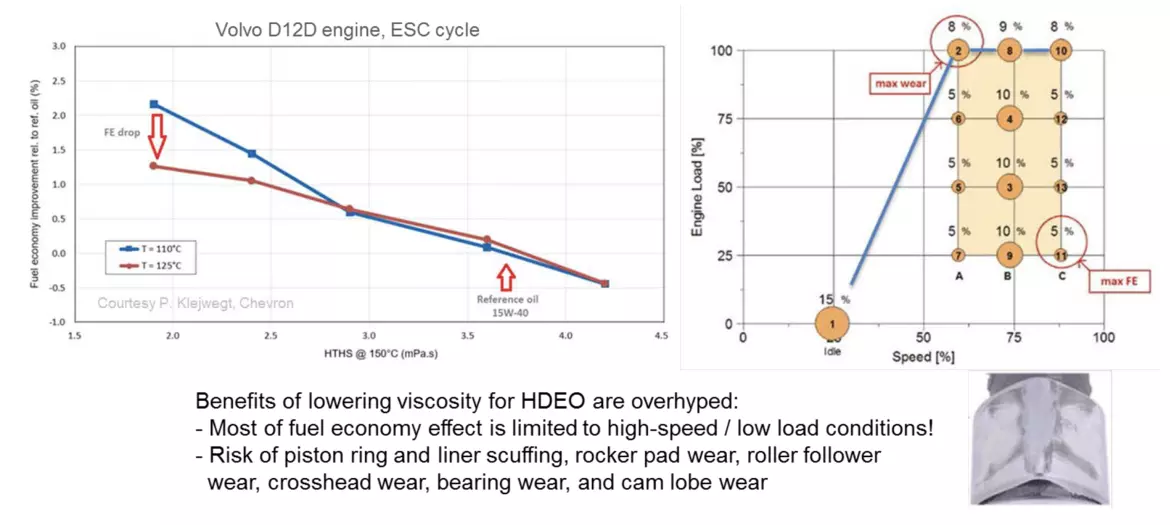
Fig.7 Migration towards fuel saving full synthetic motor oil
Friction modifiers can roughly be grouped into two major categories: (1) particulate systems (PTFE, graphite, graphene, MoS2, WS2, IF-WS2, nanoboric acid, copper/copper oleate nanoparticles, etc); (2) adsorption layer forming systems, which in their turn, can be monomolecular (glycerol mono-oleate, sorbitan mono-oleate, fatty triglycerides, esters of hydroxycarboxylic acids, phosphate esters, borate esters, fatty acids, fatty amides, fatty amines, sulfurized fats, etc.) and polymeric (methacrylates, polyesters, polyethers, polyamides, polymerized vegetable oils, etc.). The main advantage of particulate systems is in their relatively high chemical stability, while their chief disadvantage being the propensity for separation. Particulate systems tend to render lubricant formulation opaque in appearance, which is not always acceptable. A particulate friction modification system is used, for instance, in the Lubrizol 21307 engine oil additive package. Adsorption layer forming systems are numerous: there are hundreds of commercial products on the market.
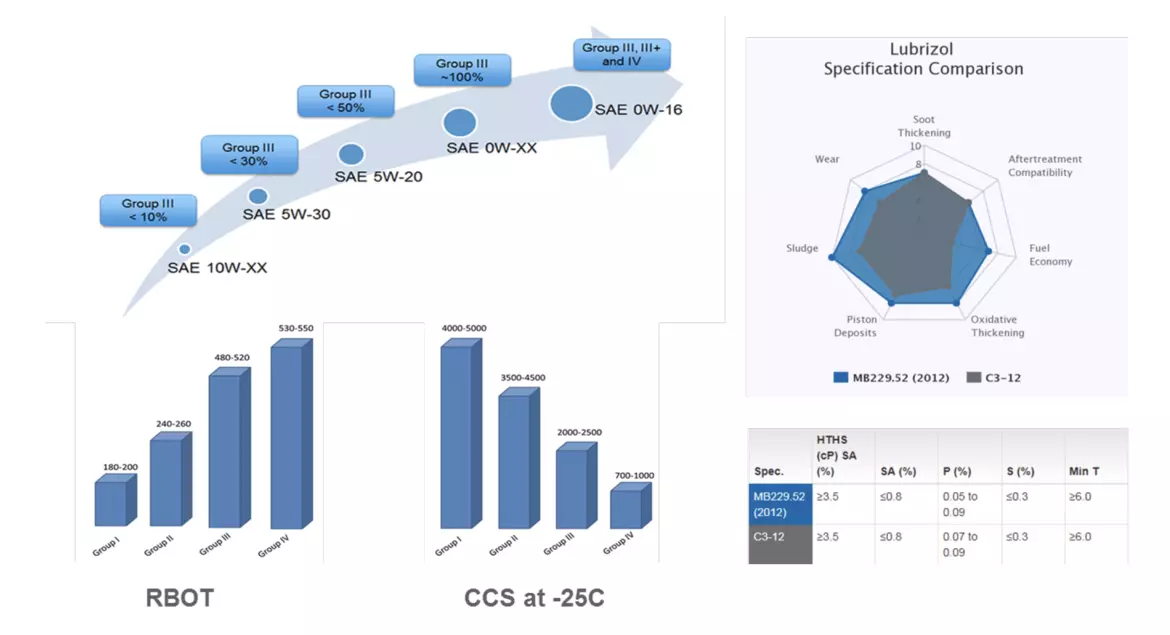
The chief difference between monomolecular and polymeric friction modifiers is the compactness of adsorbed layers. Whereas monomolecular OFMs tend to produce dense “brush-like” molecular layers, polymeric OFMs produce “gel-like” adsorption layers. These layers cause repulsion between the surfaces – the same way as polymeric dispersants do – contributing to the so-called “superlubricity” effect: they tend to shift the Stribeck curve to the left by extending the range of full-film lubrication towards higher loads [2,16]. However, they do not necessarily reduce friction in the full-film lubrication regime.
Densely packed brush-like structures seems to deliver the best friction reducing effect in laboratory rig tests, such as HFRR, pin-on-disk, Cameron-Plint, MTM, etc. On the other hand, they are more prone to displace other surface active species due to competitive adsorption. For instance, glyceryl mono-oleate may effectively displace molybdenum phosphorothioate from the surface. For the same reason, molybdenum additives lose efficiency when deployed in combination with certain ester base oils.
Mixed systems may combine superlubricity with boundary lubricity. For instance, polymerized vegetable oil usually contains small amounts of fatty acids and partial glycerol esters. The polymeric molecules provide steric repulsion between the rubbing surfaces, while fatty acids and partial glycerol esters boost boundary lubricity [17]. Many commercial OFMs systems exhibit the same property (for example, Perfad 3000 from Croda). This type of behavior can be easily simulated in laboratory tests by combining common VI improvers, such as PIB or polystyrene, with glycerol mono-oleate or sorbitan mono-oleate.
Surface gel forming OFMs are less likely to engage into competitive adsorption since they have fewer “anchors” per unit area. This allows one to develop formulations combining favorable extreme pressure properties with the “superlubricity” effect; see, for instance, Fig. 8 [18].
A similar superlubricity effect can be experienced while walking on the slippery rocks of the seashore. The algae slime growing on the rocks retains a sufficiently thick layer of water, which acts as a lubricant between your feet and the rock surface. Without this slime, water film strength would not be sufficient to support your feet. Adsorption layers formed by such surface-gel-forming superlubricity additives are viscoelastic (or pseudoplastic) and have a beneficial tribological effect as they reduce friction and wear, as well as associated energy dissipation and noise excitation. They also help solubilize particulate matter by acting as polymeric dispersants. The disjoining force between two surfaces in the presence of such additives can be directly measured using atomic force microscopy, Fig. 9 [13]
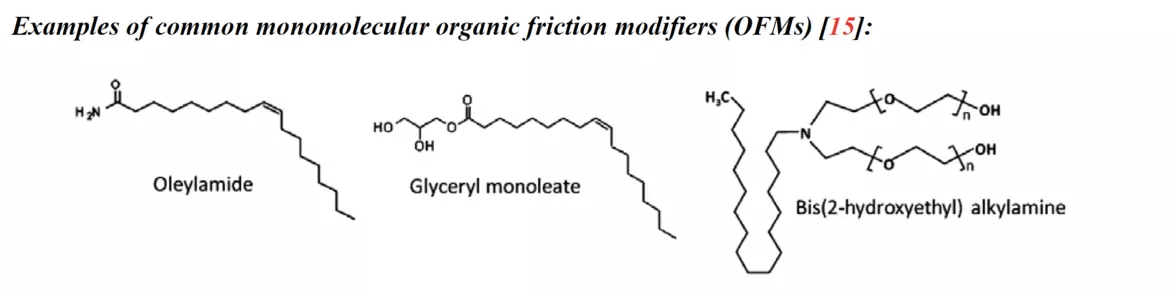
Fig.8 A synergistic friction modifier system containing a polymeric friction modifier and a moly additive [18]
Fig.9 AFM measurements showing the repulsive force due to the surface gel layer formed by a surface-active block-copolymer superlubricity additive [13]
Oil soluble inorganic friction modifiers, such as molybdenum di(2-ethylhexyl) phosphorodithioates, fatty amides of molybdic and tungstic acids, antimony dialkyl phosphorodithioate, borate esters may work in two different ways: First, they act by adsorption – and their affinity to the metal surfaces is usually higher than for OFMs. Second, they can undergo tribomutation under extreme pressure and/or shear conditions, depositing solid lubricant layers at the rubbing surfaces in contact. Thus, molybdenum derivatives are converted into MoS2, tungsten – into WS2, borate – into boric acid, etc. By doing so, inorganic friction modifiers play an essential role in the run-in process [19]. This property also serves as a basis for mechanochemical surface finishing [20] and results in reduced friction and wear, see Fig.10.
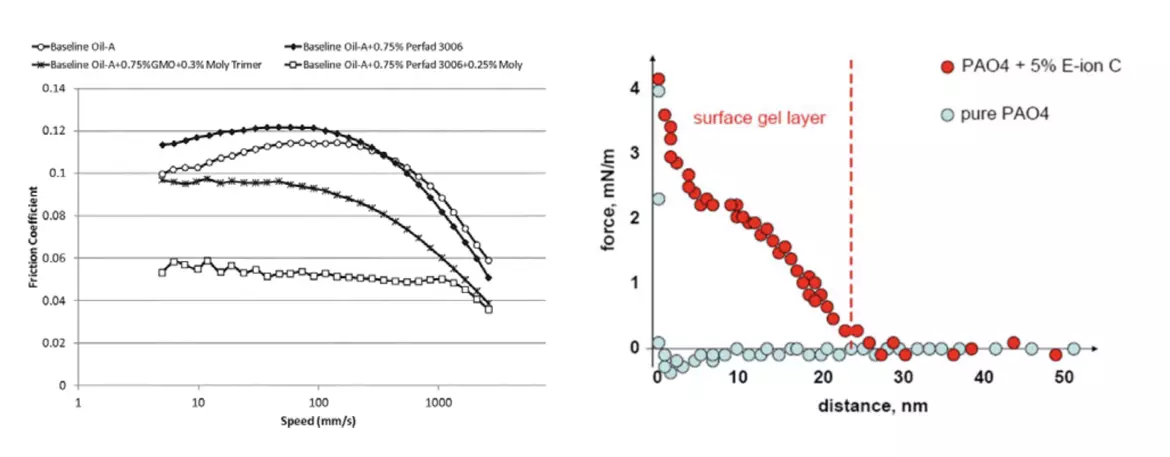
Fig.10 Effect of ZDDP and inorganic friction modifiers on valvetrain friction (after Ashworth et al. [21])
Effect of motor oil on engine friction for different engine designs
As has already been mentioned in the introduction, changing to a lower viscosity lubricant helps reduce engine friction. The best way to illustrate this is by using motored engine rigs [4,13]. Figs. 11-13 show friction torque data for two different gasoline engines. Used but functional production 2L i4 engines were used to build the rigs. The rigs were run non-pressurized, using an external pulseless electric oil pump to supply oil. Also, a heavy fly wheel was used to reduce data noise. The chief difference between the engines was the cylinder bore surface: honed cast iron vs thermally sprayed, and the valve train type: direct-acting mechanical bucket (DAMB) vs roller finger follower (RFF).
Fig. 11 shows the effect of oil temperature on engine friction. As expected, lower oil temperature is associated with higher friction. For the older engine design (Engine A: Ford Duratec) utilizing conventional cast iron cylinder bores and a DAMB valvetrain, there is a slight increase in friction in the low rpm end: this can be attributed to the hydrodynamic lubricant film collapse and excessive boundary friction in the valvetrain and the reciprocating group. For the newer engine design (Engine B: Mercedes Benz M133) with spray-coated bores and RFF valvetrain, the friction torque is nearly linearly dependent on engine speed. This shows the new design allows one effectively avert boundary friction.
Fig. 12 shows the effect of oil viscosity grade at working temperature of 90oC. Moving from the legacy SAE 10W-40 grade to 0W-16 allows nearly twofold reduction in engine friction at high rpm. However, the effect gets progressively smaller when going to lower rpm. It is interesting that for the older engine, the lowest viscosity oil gives the highest friction in the low rpm end. Once again, this shows the hydrodynamic lubricant film collapse may be a real problem.
Finally, Fig. 13 shows how engine friction responds to the use of a friction modifier in the lubricant formulation. One can see that the engine with a DAMB valvetrain and conventional cast iron cylinder bores gains more benefit from deployment of friction modifiers than the engine with an RFF valvetrain and thermally sprayed bores. This shows that the deployment of friction modifiers only makes sense when there is a substantial contribution of boundary friction in the total energy loss.
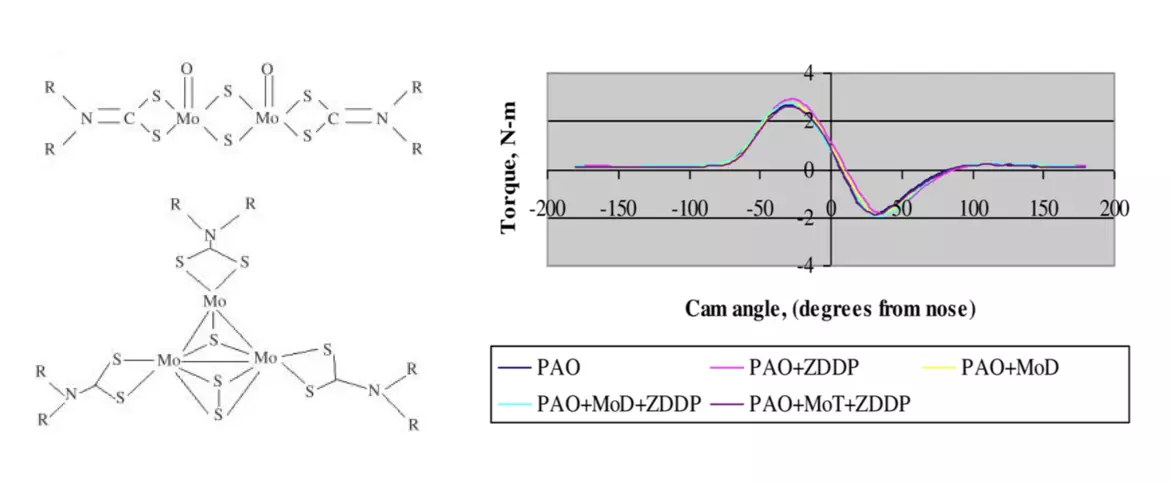
Fig.11 The effect of oil temperature on engine friction: l.h.s. - Engine A, r.h.s. - Engine B.
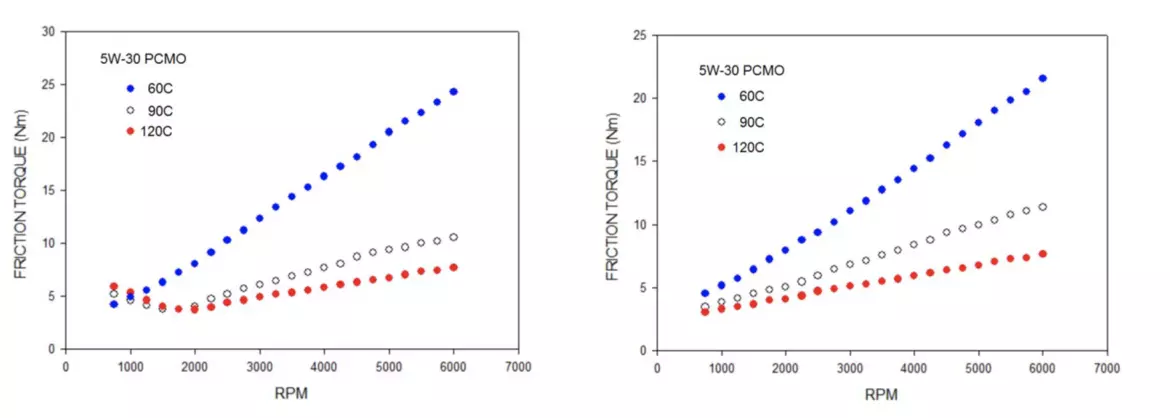
Fig.12 The effect of oil viscosity grade on engine friction at 90oC: l.h.s. - Engine A, r.h.s. - Engine B.
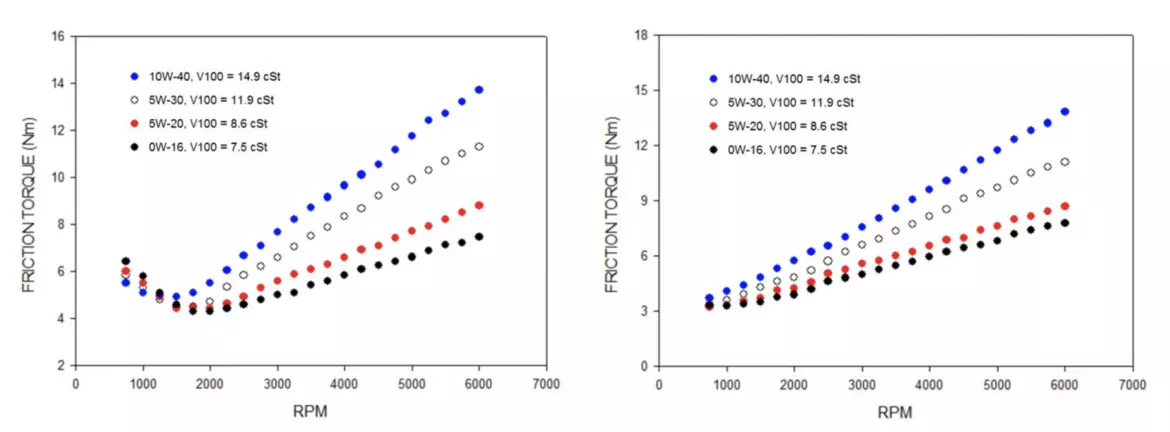
Fig.13 The effect of molybdenum friction modifier on engine friction: l.h.s. - Engine A, r.h.s. - Engine B.
It is important to understand that different friction modifiers may compete with each other for vacant surface sites, and they may also compete with another important class of additives invariably present in crankcase lubricant formulations – the detergents [22]. As a result, two different oil formulations having exactly the same viscometric properties may still have different fuel economy, although variations hardly ever exceed 1 per cent.
Some insights regarding hybrid powertrains
Hybrid powertrains bring about new challenges for oil formulators: since the ICE engine is not permanently firing during the car use, it may fail to reach working temperate. This creates conditions for water condensation on power cylinder walls, followed by water accumulation in the crankcase. Since OFMs are surface active, they help to solubilize water and drive it away from the crankcase. The powertrain control electronics must engage the ICE at intervals to heat up the oil and evaporate excess water.
Another important aspects why OFMs are so important for motor oils for hybrid cars is the additional fuel saving. Hybrids tend to use low and ultralow viscosity lubricants: from 0W-20 (Volvo, Mercedes) down to 0W-8 (Honda). Oil viscosity has the dominant effect on fuel economy in the high speed-low load limit. However, this operating regime is relatively unimportant in real life. On the other hand, OFMs help improve fuel economy in the low speed-high load limit that lies closer to the engine sweet spot and is the most interesting from a practical point of view. Besides that, OFMs help minimize dependence on inorganic friction modifiers that may be potentially harmful for the exhaust control equipment. Fig. 14 shows that organic friction modifiers can successfully compete with MoDTC in terms of the friction reducing effect.
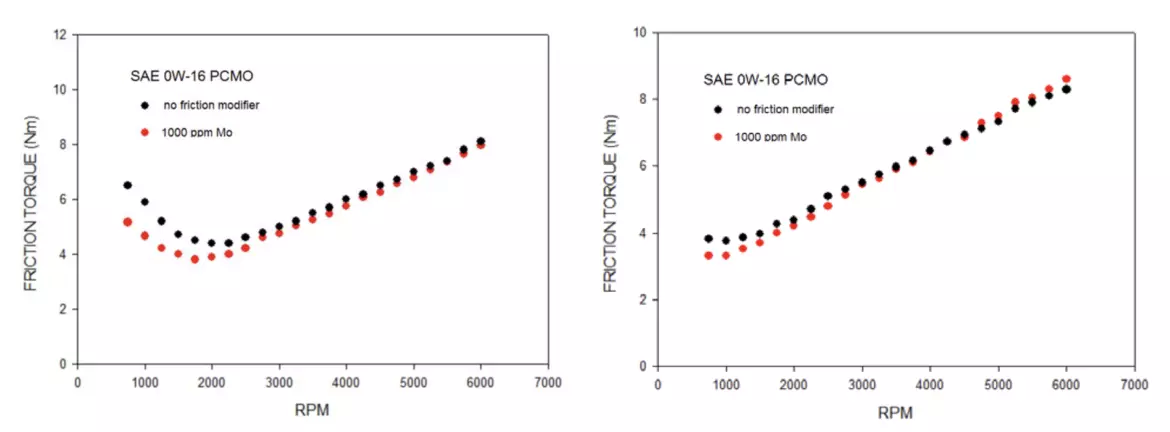
Fig.14 MTM test data comparing two commercial organic friction modifiers with MoDTC in PAO base oil. The following test conditions were used: SRR 50%, load 36N, temperature 100oC.
Last but not least: polymeric OFMs works nicely in combination with oil soluble polyether (OSP) and ester base oils that are often used in ultralow viscosity lubricants (0W-8 and 0W-12 grades), whereas molybdenum additives turn out to be less efficient in this case.
In Japan, the move to SAE 0W-20 oil began already around 1980, and the first SAE 0W-16 like product (there were no J300 designations for sub SAE 20 viscosity grades at that time) was introduced in 2010. Nowadays, Honda and Toyota actively promote the SAE 0W-8 technology that brings on average 3-4% improvement in fuel economy over SAE 0W-20. The new JASO Fuel Economy Test has been developed and will possibly replace the existing Sequence VIF in the future ILSAC GF-7 specification. The development of the new standard – known as JASO M364:2019 – and oil specification – JASO GLV-1 – has been completed in 2019 [23]. For the fuel economy test, either the firing Toyota 2ZR-FXE 1.8L engine or motored Nissan MR20DD 2.0L engine can be used. The proposed fuel economy limits for the new JASO GLV-1 specification are >1.1% (firing) and >2.0% (motored) compared to SAE 0W-16 reference oil. ILSAC GF-7 is not likely to come before 2025 - if it comes at all, taking into account all the hurdles, delays, prohibitive cost and limited usefulness of ILSAC GF-6 category.
Concluding remarks
Motor oil is an important element in the development of low friction powertrains. Switching to low viscosity motor oil is an efficient way to reduce friction losses in internal combustion engines. However, low viscosity oil tends to compromise wear protection necessitating deployment of friction modifiers and antiwear additives in crankcase lubricant formulations. Together with a broader adoption of synthetic base oils, friction modifiers are expected to play an increasingly important role in future.
Conflict of interest
The authors declare that the research was conducted in the absence of any commercial or financial relationships that could be construed as a potential conflict of interest.
Author contributions
Boris Zhmud stands behind the general article idea and research data. Arthur Coen and Karima Zitouni have contributed to the section about the use of various classes of friction modifiers.
Acknowledgements
Robert Ian Taylor is thanked for inspiring discussion and comments regarding the motored engine friction tests. Peter Klejwegt is thanked for sharing his experience with fuel economy engine oil for heavy duty applications.
References
- K. Holmberg, P. Andersson, A. Erdemir. Global energy consumption due to friction in passenger cars. Tribology International, 47 (2012) 221.
- B. Zhmud, Developing energy-efficient lubricants and coatings for automotive applications, Tribology and Lubrication Technology 67(9) (2011) 42.
- B. Zhmud, Pursuit for better fuel economy: Reducing engine friction helps maxing out miles per gallon, The Vehicle Component 5 (2012) 18.
- R.I. Taylor, N. Morgan, R. Mainwaring, T. Davenport, How much mixed/boundary friction is there in an engine - and where is it? Proc IMechE Part J: J. Engineering Tribology 234 (2020) 1563.
- B. Zhmud, Engine tribology: a thorny way from lab to field, Lube 154 (2019) 20.
- R.I. Taylor, R.C. Coy, Improved fuel efficiency by lubricant design: A review, Proc. Inst. Mech. Eng. 214 (1999) 1.
- B. Tatievski, B. Zhmud, "Fuel economy engine oils: Scientific rationale and controversies", in Proc. 20th International Colloquium Tribology, Stuttgart, Germany, January 12-14, 2016.
- D.E. Sander, H. Allmaier, C. Knauder, F. Strömstedt, Potentials and risks of reducing friction with future ultra-low-viscosity engine oils. MTZ Worldwide 79 (2018) 21.
- P. Kleijwegt, R. ter Rele, M. Sabater Ferret, R. van den Bulk, ”Global heavy-duty engine oil specifications and their impact on current and next generation lubricants” Benelux Smeermiddelen Congres, Retie, Belgium, 26 Sep 2019.
- G. Lechner, A. Knafl, D. Assanis, S. Tseregounis, M. McMillan, S. Tung, P. Mulawa, E. Bardasz, S. Cowling, Engine oil effects on the friction and emissions of a light-duty, 2.2L direct-injection diesel engine, Part 1 - Engine test results. SAE Technical Papers 2002-01-2681.
- S. Tung, M. McMillan, G. Hong, E. Bardasz, Engine oil effects on friction and wear using 2.2L direct injection diesel engine components for bench testing, Part 2: Tribology bench test results and surface analyses. SAE Technical Papers 2004-01-2005.
- B. Zhmud, E. Tomanik, “Optimizing the piston/bore tribology: The role of surface specifications, ring pack, and lubricant.” International Colloquium Tribology, Esslingen, Germany, January 28-30, 2020.
- B. Zhmud, B. Tatievski, “Preparing for ILSAC GF-6: Advantages of full-synthetic motor oils for boosting fuel economy.” World Tribology Congress, Beijing, China, Sep. 17-22, 2017.
- B. Zhmud, “Current advances in crankcase lubricants.” European Base Oil & Lubricants Summit, Rotterdam, The Netherlands, Nov. 20-21, 2019.
- H. Spikes, Friction modifier additives, Trib. Lett. 60 (2015) 5.
- B. Zhmud, M. Roegiers, New base oils pose a challenge for solubility and lubricity, Tribology and Lubrication Technology 65(7) (2009) 34.
- M. Roegiers, B. Zhmud, Tribological performance of ionized vegetable oils as lubricity and fatty oiliness additives in lubricants and fuels, Lubrication Science 21 (2009) 169.
- M.C. Southby, H. Gao, C. Chen, C.A. Chin, B.L. Parke, Lubricating composition, WO Patent 2015193395, 23 Dec. 2015.
- S. Li, R. Zhang, Y. Jin, Y. Wang, S. Tung, Tribocarbonisation of a synthetic engine oil in lubricated piston ring/cylinder bore sliding contact and its relation to friction and wear. Journal of Synthetic Lubrication 20 (2003) 203.
- B. Zhmud, "In-manufacture running-in of engine components by using the Triboconditioning® process", in M. Abdel Wahab (Ed.): FFW 2018, LNME, pp. 671–681, 2019.
- S. Ashworth, K. Mistry, A. Morina, A. Neville, Single cam tribometer for evaluating tribological parameters and tribochemistry of DLC coated valve train follower. Tribology - Materials, Surfaces & Interfaces, 6 (2012) 31.
- S. Li, R. Zhang, Y. Jin, Y. Wang, S. Tung, Competitive surface interactions of critical additives with piston ring/cylinder liner components under lubricated breaking-in conditions. Tribology Transactions 46 (2003) 200.
- S. Yoshida, K. Yamamori, S. Hirano, T. Sagawa, et al., The development of JASO GLV-1 next generation low viscosity automotive gasoline engine oils specification. SAE Technical Paper 2020-01-1426
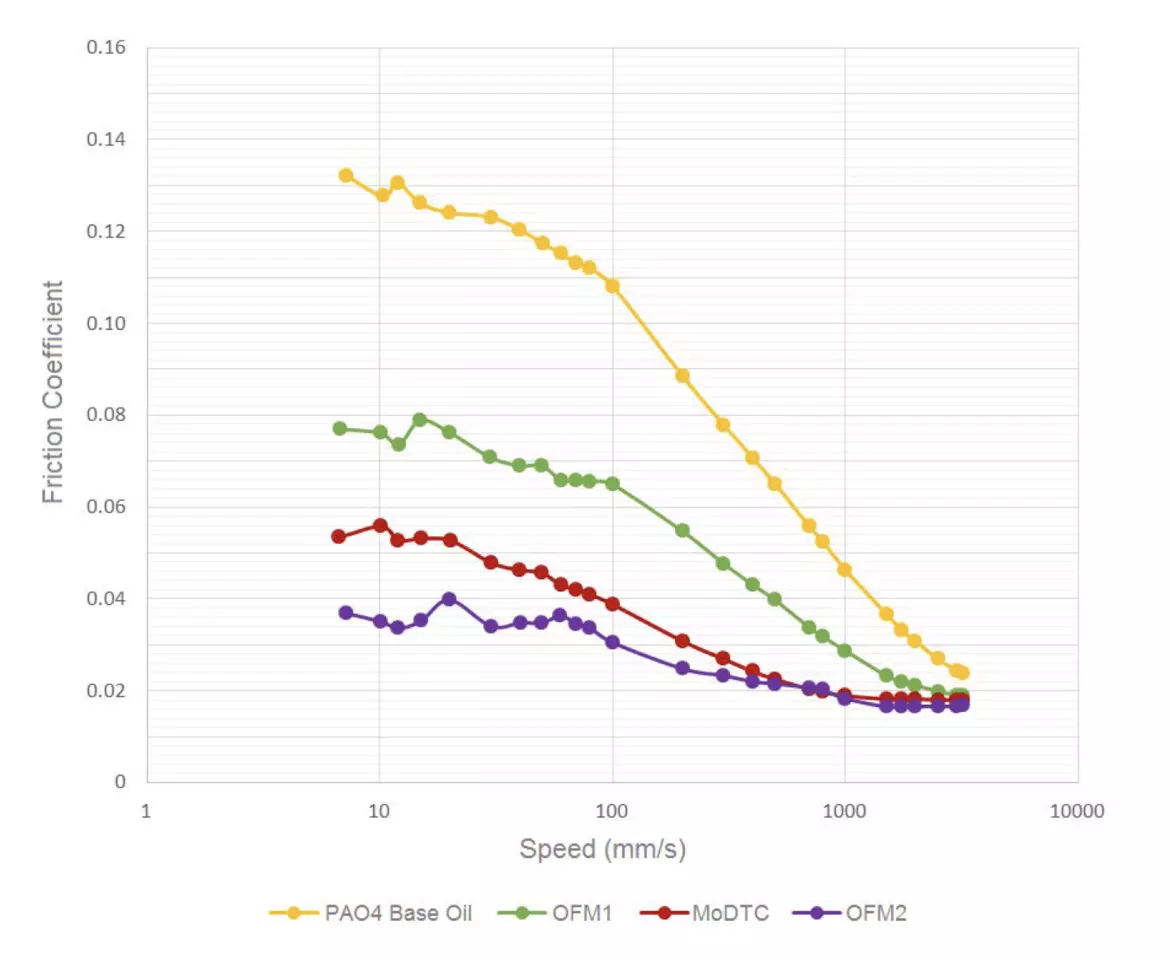
You might also like
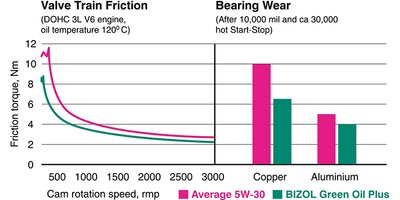
Prof. Dr. Boris Zhmud, Head of R&D, BIZOL Germany

Within the realm of automotive care, few substances are as vital as motor oil, in ensuring the seamless operation of a vehicle's propelling device. It serves as the lifeblood of a motor, ensuring that the intricate machinery operates efficiently and without unnecessary friction. The functions of motor lubricant substance extend far beyond just lubrication, encompassing a range of critical tasks that contribute to the longevity and performance of a propelling mechanism. In this article, we’ll delve into the multifaceted functions of motor oil and explore how it plays a pivotal role in maintaining the health of automotive powerhouses.

The modern marvel of an internal combustion motor powers our vehicles, providing the strength and reliability we rely on for daily transportation. However, just like anything else subjected to constant use, motorized units experience wear and tear over time. Component deterioration can significantly impact performance and longevity. In this article, we will delve into the intricacies of engine wear meaning, explore the various causes behind it, provide actionable tips to reduce and prevent it. Furthermore, we will look at how specialized engine oils, such as BIZOL, play a crucial role in safeguarding your engine’s health. Let’s begin by understanding what engine wear is and the factors that contribute to it.